Work
underground was quite varied. Tasks to be carried out
included drilling, plate laying, timberwork, machinery
operating and cleaning up. The mine was cut on different
levels, each one numbered. Interestingly, only even
numbers were used. Levels which were being mined for ore
were called production levels, whereas tunnels being
prepared were known as developmental levels.
At the start of each shift, men had to
clear away the rubble left behind by the previous shift
before they could start their own digging. The ore was
scraped out of the working area (the stope) by a
dragline and scoop. It was forced through an iron grid
(grizzly) into tram trucks, then driven to a loading
pocket, tipped into a 5 ton skip and hoisted to the
surface.
All the while, miners drilled holes
for each firing. Some used existing holes from the
previous firing, with grave risk of unexploded dynamite
from the previous shift. This was not allowed, but some
did take the chance, with sometimes fatal results. A
mechanical digger (bogger) was used to expose the ore
wall for drilling and to scrape away the waste. A
special method of drilling a series of holes with
explosives timed in a certain sequence made sure the
tunnels were made to the correct size, usually 8 feet by
8 feet. Plate-layers laid track for the trams, so that
waste (mullock) could be trucked away. Other workers
laid electric cables and air pipes while timbermen
shored the walls of the tunnel. The timber was pre-cut
above ground so that construction underground was made
easier. At the start, the company only used Canadian
oregon pine for this, as local Australian hardwoods
cracked and collapsed without warning. The oregon pine
made creaking noises before giving way, allowing workers
time to evacuate before a collapse occurred. The
imported timber became too expensive after a time and
other more local timbers were used.
Meals were eaten underground in
special areas for the purpose (crib cuddys). These had
benches, tables and electric urns and men could cook
meals using steamers. At the end of each shift, the
firing took place. The shift boss loaded the men from
the lowest level into the cage at 3.20pm and fired the
charges. The firing commenced on the lowest level then
on each level to the topmost one. The ventilation system
cleared the dust within 40 minutes and the afternoon
shift was lowered down the shaft to start the process
all over again.
The ore was carried to the surface in
a 5 ton skip, where it was dumped into an ore bin. From
there it was moved into crushers where it was made into
gravel, then stored in 4 large silos each holding 1,000
tons. Vibrators in the silos ensured the ore travelled
smoothly onto conveyor belts taking it to ball mills,
further reducing the ore to a powdery consistency. After
passing through classifiers, the various elements were
separated using an oil-flotation method. This process
became the standard method for processing ore after its
invention in Broken Hill. It worked by mixing certain
chemicals with the ore in contact with oil. The
chemicals attached themselves to all but one mineral
which floated to the top to be skimmed off. First
removed was the lead concentrate which yielded lead,
gold, silver and copper upon smelting. After the lead
concentrates came zinc and lastly, iron pyrites used for
making superphosphates and sulphuric acid. Once the
minerals had been extracted, the wastes were channelled
into large holding dams where the heavier materials sank
to the bottom and the water evaporated. Later a
different method was used where the water was mostly
removed from the sludge first and the solids dumped onto
a waste hill.
Mining is a dangerous profession. Men
are totally reliant on the structure of the tunnels they
create. The more tunnelling which takes place, the less
stable the structure becomes. Levels down to 2,600 feet
had been dug by 1961 with such serious structural
movements on a number of levels, all miners were
evacuated from them. At the southern end of the mine
ridge, an entire section collapsed prompting the company
to post warnings as to the dangers of walking there.
Three such collpases happened in that area which was
known as Keatings.
The nature of the geological structure
of the hills meant that rain leaked through and ran down
into the filling passes, further destabilising the
drives. At times this water literally poured down the
tunnel walls and water hosing to settle dust also made
conditions unfavourable. Fallen ore was collected by men
in wet weather clothing and boots under the passes and
pumps worked to draw the water away.
Waste holding dams collapsed on more
than one occasion, seriously polluting the river system
and the reservoir. The water from the reservoir was used
for mining, drinking underground as well as for workers'
showers. Mine managers assured the miners that the water
was perfectly safe, but men refused to work until this
was proved.
The mine had many serious accidents
over its period of operation, with men killed and
injured. Statistically, one man died for every year the
mines were in operation. |
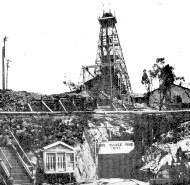
The mine head and poppet in 1959
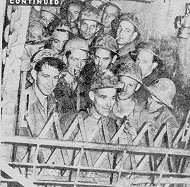
Men loaded into a cage to go underground
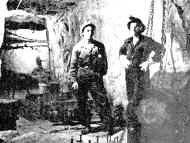
Workers installing equipment underground
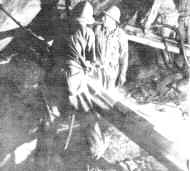
Working at the top of the stope
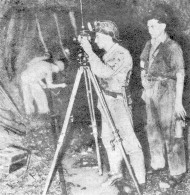
Using a theodolite underground to check levels
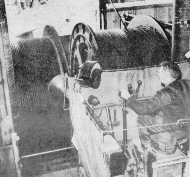
Working in the engine room
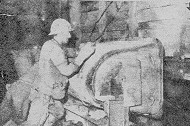
Tipping ore from a train down a grizzly for loading
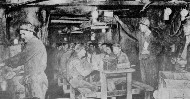
Men ate meals underground. These rooms (or cribs) cut
from solid rock had hot water, electric lights and a
wash trough
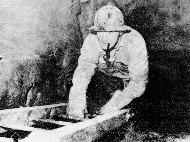
An engineer climbs a steel ladder to the top of a stope |